Seguramente si vas a leer este tocho es por que nadie te va a parar en tu empeño de fabricar tu propia tabla, y estas dispuest@ a hacerlo cueste lo que cueste. Si esto es así este es el lugar adecuado para empezar tu aventura de shaper, una aventura apasionante en busca de la perfección en el diseño, del peso y las características de tu futura creación, una tabla de surf.
Para empezar hay que señalar que la fabricación de una tabla de surf no es una tarea fácil, necesitas tiempo, los materiales adecuados, paciencia, y cierto talento para que el diseño de la tabla quede perfecto. Pero no desesperes, no es una misión imposible, solamente tienes que seguir los pasos adecuados.
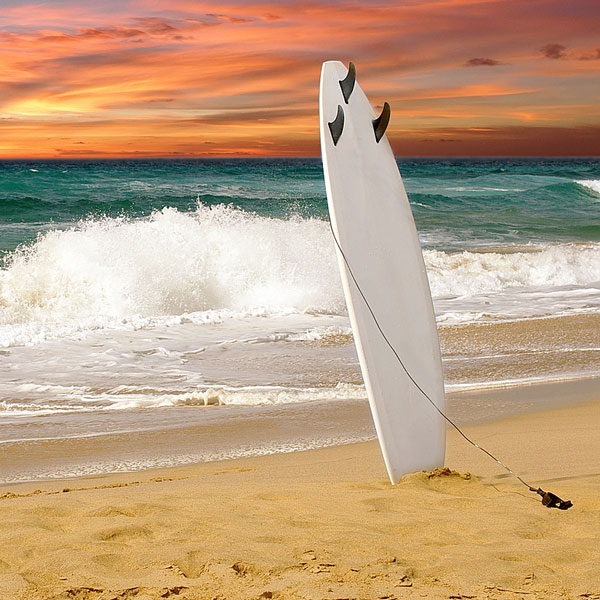
El paso previo al diseño es el conocer las características que debe tener una tabla de surf dependiendo de las olas que se van a surfear, el peso y el nivel del surfer que la va a utilizar. No es lo mismo una tabla de iniciación que una para un surfer ya experimentado. Puedes encontrar completa información sobre estos factores en el artículo anatomía de una tabla de surf, también es aconsejable examinar cuidadosamente el diseño de tablas fabricadas por shapers profesionales, la forma de los cantos la cola, el rocker, la distribución de las quillas, etc.
Una vez que tengas claro estos factores y hayas decidido que forma va a tener tu futura creación, dibújala sobre papel y anota las medidas del alto, ancho, grosor, punta y cola, así como otras características que vayas a incluir en el diseño.
01. El lugar de trabajo
La elección y preparación adecuada del lugar donde se va llevar a cabo la fabricación de la tabla es muy importante para facilitar el proceso, y evitar posibles peligros y molestias.
Es aconsejable que el lugar sea una habitación suficientemente amplia y despejada de cosas que puedan entorpecer nuestra movilidad. Es muy importante que esté bien ventilada durante todo el proceso ayudándote, si es necesario, de un ventilador para expulsar los vapores de la resina de poliéster.
El lugar donde trabajaremos la tabla serán dos soportes con forma de u al final acolchadas para evitar daños en el foam y colocados la altura de la cintura.
Deberá haber un tubo fluorescente a la altura del pecho colocado en una pared cercana al lugar de trabajo y con una mampara para que no nos de la luz en la cara, esto es para ver con facilidad los relieves del foam en el momento del shapeado, para ello también es aconsejable que las paredes no sean blancas.
Hay que disponer una zona de la habitación para poner los materiales de forma ordenada y fácil de encontrar.
Debes hacer especial hincapié en la limpieza del lugar, quitando la suciedad y el polvo de foam o resina después de cada jornada de trabajo.
02. Los materiales
Cuando tengas planteado y anotado el diseño de la tabla es el momento de hacerte con los materiales necesarios para llevar a cabo tu misión.
Estos materiales se pueden dividir en tres grupos, Materia Prima, Herramientas, y Material de seguridad:
La materia prima, esto es, los materiales de los que están fabricados las tablas de surf:
•El Foam. El foam es el material del interior de la tabla de surf. Es una espuma muy ligera y maleable con un refuerzo de madera (alma) que recorre el centro longitudinalmente para aumentar la rigidez de la tabla. El tipo de foam más usado es el de la marca “Clark Foam”, que viene de fábrica con cierta curvatura y forma para que el shapeado sea más fácil. Se consigue en distribuidores especializados, o desde su Web https://www.clarkfoam.com
•La fibra de vidrio. Es el material que junto a la resina de poliéster cubre al foam y su función viene a ser como el armazón metálico en el hormigón armado. Este material es un tejido de hilos de fibra de vidrio con un tramado que entrelaza los hilos verticales con los horizontales e incluso en algún tipo de fibra el hilo va torsionado sobre sí mismo para aportar más rigidez. Este tejido puede tener distintos grosores, lo normal es usar telas de 4 onzas. “Hexcel” es un prestigioso fabricante de fibra adecuada para las tablas, https://www.hexcel.com
•La resina. Es un material gelatinoso y transparente que en reacción con el catalizador se endurece. Podemos usar dos tipos de resinas, la de poliéster, más económica y más común y la de epoxi, más dura, lo que nos permite aplicar menos cantidad y así aligerar el peso final. Es aconsejable usar resinas de calidad y que no amarilleen con el tiempo como la de la marca “Silmar”, https://www.interplastic.com. El disolvente que nos quitará las manchas de resina es la acetona.
•Catalizador. Es el endurecedor de la resina, que en la de poliéster se mezcla al 2% y en la de epoxi al 40%, porcentajes que pueden variar algo según el fabricante.
•Tapón del invento y quillas. Estos componentes se suelen comprar ya fabricados en distribuidores o tiendas de surf especializadas.
Herramientas, de las que nos serviremos para dar forma y manipular la materia prima:
•Cepillo eléctrico. Es la herramienta que sirve para dar forma al foam. “Clark Foam” distribuye y recomienda el modelo P20-SB modificado deHITACHI https://www.clarkfoam.com/info-equipment.htm.
•Lija de malla. Especial para dar la forma a los cantos en el foam.
•Calibrador para el grosor
•Cinta métrica.
•Serrucho o sierra de calar.
•Lápices, papel y plantillas
•Aplicador de resina. Una paleta de goma en forma rectangular que ayuda a extender la resina de poliéster.
•Envases y medidores para la resina
•Lijadora Eléctrica. Una lijadora convencional para el desbastado y pulido de la resina de poliéster.
•Papel de lija de agua con varios gruesos para dejarla paso a paso lista para el pulido.
•Taladradora – fresadora para colocar el tapón del invento y los tapones de las quillas si son de quita y pon. Material de seguridad. Algunos componentes de la tabla de surf necesitan que nos protejamos para su tratamiento o aplicación, como ocurre con los vapores de la resina de poliéster y el polvo resultante del lijado del foam, que pueden ser tóxicos por inhalación.
•Mascarilla protectora.
•Gafas Protectoras.
•Guantes de latex.
03. Preparar el Foam
El paso previo a shapear el foam es hacer una plantilla con la forma de la tabla, pero sólo la mitad longitudinal de la tabla desde el centro hasta el borde, es como si tuviésemos sólo la parte izquierda o derecha de la tabla.
Para hacer la plantilla puntearemos las medidas (sólo la mitad) que queremos en nuestro diseño: centro (aunque suele coincidir no tiene que ser el punto más ancho), proa 12 primeras pulgadas y popa 12 primeras pulgadas, estas coordenadas las uniremos con la línea curva que conformará el outline de nuestra tabla.
Colocamos esta plantilla encima del foam y con un lápiz dibujamos el contorno de la plantilla sobre el foam en la parte izquierda y derecha por igual.
Con un serrucho o una sierra de calar cortamos los sobrantes del foam bruto siguiendo la línea que hemos dibujado con la plantilla.
De este modo ya tenemos el outline de nuestra tabla plasmado en el foam y preparado para el shapeado.
04. Shapeado
Este es el proceso más delicado, ya que de él depende la calidad y el rendimiento de nuestra futura tabla de surf.
Se empieza desbastando el foam con el cepillo eléctrico por ambas caras de la tabla, profundizaremos lo justo para dar la curvatura y el grosor deseado a la tabla, tras esto se le da cierta curvatura a los cantos, pero sin profundizar mucho en ellos. El cepillado ha de hacerse con movimientos longitudinales a lo largo de la tabla, nunca a lo ancho.
Hay que tener en cuenta que esta primera fase del shapeado se realiza con una máquina que no deja muy buen acabado, por lo tanto se trata tan solo de desbastar el foam y prepararlo para el trabajo realmente delicado que se realiza a mano. Es por esto que no hay que ahondar mucho con el cepillo, ya que un error podría hacernos perder el foam.
Cuando hayamos terminado de trabajar con el cepillo eléctrico usaremos lija de malla que tiene unas perforaciones que permite evacuar el polvo de foam resultante con más facilidad. Para ello envolveremos la lija en una pieza de madera o plástico plano como aparece en la foto.
Iremos dando la forma final a la tabla gradualmente, suavizando las curvas, igualando los lados. Este es un trabajo largo y laborioso hasta lograr un buen resultado final.
Es necesario mirar al ras la superficie del foam para detectar imperfecciones e ir eliminándolas
05. Acabando la forma
En el acabado del shape se debe revisar y perfeccionar cada curva y eliminar cada pequeña irregularidad con una lija de malla fina. También se debe rebajar el alma para que quede completamente al nivel del foam.
Una vez terminada la forma se sacudirá todo el polvo de foam que se encuentre en la tabla y se dejará lista para el glaseado.
Este es el momento para firmar tu creación, generalmente en la parte del fondo junto al alma, aquí se ponen las medidas de la tabla (altura, ancho y grosor) y tú firma.
06. Señalado de la ubicación de las quillas.
Con el lápiz trazaremos sobre el foam el lugar donde vamos a colocar las quillas. Si las quillas son fijas son dos puntos coincidiendo con los extremos de la base de la quilla. Si las quillas son de “quita y pon” seguiremos la recomendación del fabricante.
El trazado de la quilla central no presenta mucha dificultad, sin embargo para las quillas laterales emplearemos un cartabón para trazar exactamente la distancia que queremos, tomando como referencia el alma de la tabla. Tendremos en cuenta además que las quillas laterales no van paralelas al alma, sino un poco inclinadas hacia el centro.
07. Glaseado
Se empieza cortando las telas de fibra de vidrio que vamos a necesitar. Generalmente se ponen dos capas en la parte superior y cantos, y una abajo, esto es así para dar más dureza a la parte superior y evitar así abollarla con nuestro peso, el fondo al estar solo en contacto con el agua únicamente necesita una capa.
Al poner más capas de fibra de vidrio, o una fibra de vidrio de mayor grosor, conseguimos darle más dureza a nuestra tabla pero a su vez le estamos dando mas peso. Hay que encontrar el equilibrio adecuado dependiendo del peso del surfer.
Una vez que tenemos los trozos de fibra de vidrio cortados con las medidas de la tabla, empezamos a trabajar sobre la parte superior de la tabla poniendo la primera capa.
Extenderemos la primera tela de fibra de vidrio a lo largo de la tabla y cubriendo toda la superficie desde la punta a la cola, así como los cantos y un trozo de la parte del fondo.
Una vez que tengamos fijada la tela prepararemos la resina para la primera capa. Depositamos en un recipiente la cantidad de resina proporcional a la superficie que tenemos que cubrir, la mezclamos con el catalizador en la proporción adecuada y removemos hasta asegurarnos que el catalizador se ha mezclado completamente con la resina.
El glaseado se realiza siempre empezando por el centro de la tabla, extendiendo la resina con el aplicador (pieza rectangular de goma) hacia los cantos y adentrándose un poco en los bordes del fondo.
Hay que asegurarse que la capa de resina sea uniforme en todas las partes de la tabla, sin zonas con más resina que otras.
La segunda capa de la parte superior se pondrá cuando la resina de la primera capa esté seca. Para la segunda capa se repetirá el proceso como se realizo en la primera capa, se extiende la tela de fibra de vidrio, se fija, y se aplica la resina.
En el fondo se hace del mismo modo que en la parte superior, pero solo se pone una capa. Esto lo haremos cuando la parte superior este seca.
08. Lijado
Una vez completamente seca la resina, se puede pasar a lijar la superficie de la tabla de surf. Para ello empezaremos con la lijadora eléctrica, una vez lijada toda la tabla a máquina pasaremos al lijado manual, para ello emplearemos al principio una lija gruesa y con ella repasaremos bien toda la superficie de la tabla. Posteriormente iremos reduciendo el grosor de la lija de agua hasta llegar al papel de lija más fino, dejando así la tabla lista para el siguiente paso, que es el pulido. Para el lijado con lija de agua, la superficie de la tabla debe estar mojada para facilitar el trabajo de la lija y un acabado más perfecto.
09. Pulido
Para realizar un buen pulido será suficiente cambiar la lija de la máquina eléctrica por el accesorio para pulir, impregnaremos la superficie de la tabla con el producto de pulimento y pasaremos concienzudamente la máquina hasta que tenga un buen acabado, tras esto limpiaremos la tabla de los restos del producto que hemos usado para pulirla
10. Colocar quillas y tapones
Este paso puede ser previo o posterior al lijado y pulido, si las quillas son fijas es muy recomendable ponerlas después del glaseado y si son de “quita y pon” nos es indiferente colocar el sistema de anclajes antes o después.
En el caso de las quillas fijas las pegaremos con superglue sobre las marcas que previamente hicimos en el foam antes de su glaseado, tras asegurarnos de que el ángulo de apertura que le hemos damos a las quillas laterales es el que queremos y que la quilla central está completamente recta colocaremos en la base de cada quilla y a ambos lados varios hilos gruesos de fibra de vidrio que sobresalgan un poco por delante y por detrás, estos los impregnaremos de resina, posteriormente le pegaremos dos telas de fibra de vidrio a cada lado de cada quilla, la primera de forma redondeada y con el diámetro un poco mayor a la base de la quilla, con el cual coincidirá en el momento de pegarla, la segunda tela tendrá forma rectangular y por un lado sobrepasará la medida de la tela redonda y por otro cubrirá la quilla completamente de forma que la parte sobrante se pegue con la de la otra cara, cuando seque la resina cortaremos este exceso hasta llegar más o menos un centímetro de la base, a partir del cual le dejaremos la forma de una curva suave hasta llegar a más o menos otro centímetro, esta vez desde la base de la quilla. En esta parte, antes del lijado y el pulido le pasaremos una lima redonda para terminar de darle la forma adecuada.
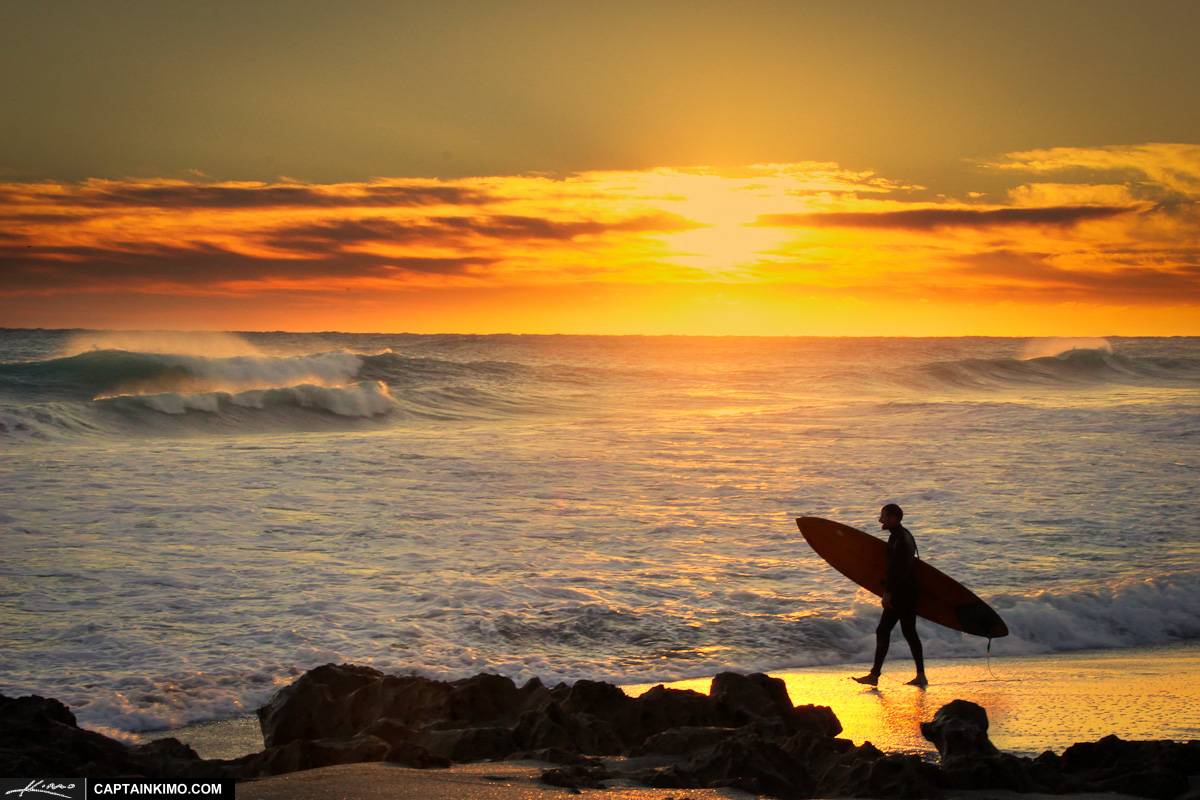
El tapón del leash y los anclajes si nuestras quillas son de “quita y pon” los ubicaremos en un hueco que practicaremos con una fresadora sobre las señales que pusimos previamente en el foam indicándonos la ubicación de cada uno.
En cuanto al hueco del tapón del leash lo fresaremos con un par de milímetros más de la medida del tapón,
posteriormente le pondremos algo de fibra de vidrio y la resina suficiente para que al meter el tapón boze tan solo un poco, exceso que eliminaremos cuando esté seca.
En cuando a los anclajes de las quillas de quita y pon tendrás que seguir las instrucciones y emplear los materiales recomendados por el fabricante.
Actualmente la gran mayoría de tablas se hacen con máquinas que con sólo meter unos parámetros te hacen los panes o foam con terminaciones perfectas ajustando todo al milímetro, ¡es el futuro!¡Tablas perfectas!
Siempre será más cómodo comprarse una de estas tablas pero por si alguien se anima a fabricarse su propia tabla este post os puede servir de mucha ayuda.
What's your reaction?
0Cool0Bad0Lol0Sad